The power compact TLM filling system with cobots
- Very compact machine design
- Feeding of the packaging components by cobots
- Built with hygienic design in mind
Requirements
Diverse formats, diverse requirements
At Börlind’s production facilities, the wide and very diverse range of natural care products for face, body and hair, which all contain plant extracts from organic cultivation and the company’s own deep spring water, without using any animal extracts, are filled into glass bottles, plastic bottles and glass jars with different types of closures and caps. The very extensive product range with many different formats makes the filling of cosmetic products a unique challenge. The company needed a new system with a high output density and a high degree of automation.
In addition to cosmetics with varying consistencies and viscosities, there are also two-phase products whereby, for example, an oil-containing and a water-containing part need to remain visually separate from each other, as well as formulations containing alcohol. This required the new system to be designed in accordance with the ATEX explosion protection directive for ‘pure’ or alcohol-containing products. Börlind also wanted the cream jars to be checked for glass breakage before the actual filling process. This is essential to ensure that the film for sealing and protecting the cosmetics can be precisely applied to the glass rim of the jars. The filling system also had to be built to ensure a hygienic design and to enable CIP cleaning (cleaning in place) without prior dismantling in a circular or continuous process. Despite the simultaneous processing of different cosmetic jars and bottles on a single system, the requirement was to keep the costs for changing format parts low. As a manufacturer of natural cosmetics, sustainability was also a key issue for Börlind, which is why the company favoured a very compact design.
Solution
New TLM filling line: Maximum performance in the smallest of spaces
Schubert met Börlind’s diverse requirements with an innovative and fully automatic TLM filling line. The glass jars, glass bottles or plastic bottles are blown out, checked, filled with the liquid cosmetics, closed and sealed with a variety of pump systems and lids – all in the smallest of spaces. The space-saving design is enabled by a recently developed multi-transport unit (MTA), which transfers the products from one station to the next during the packaging process. Daniel Traub, Global Key Account Manager at Schubert, explains: “A compact machine layout is a key factor for the ecological footprint, as it allows energy consumption to be kept lower than with large-scale linear systems.”
The individual components of all packaging formats are fed by three tog.519 cobots, so the automation begins upstream of the machine and supports the line’s high output density of up to 60 products per minute. The customised 3D-printed format tools, which Börlind can reprint in its own facilities using Schubert’s PARTBOX system, similarly to all other format parts on the line, ensure a secure grip, and enable new formats to be availablequickly and cost-effectively. The modular machine concept also provides significant benefits, as additional process steps can be added directly to the filling line. For example, the labelling of the filled and sealed cosmetic packaging as well as the final packaging can be integrated into one complete line.
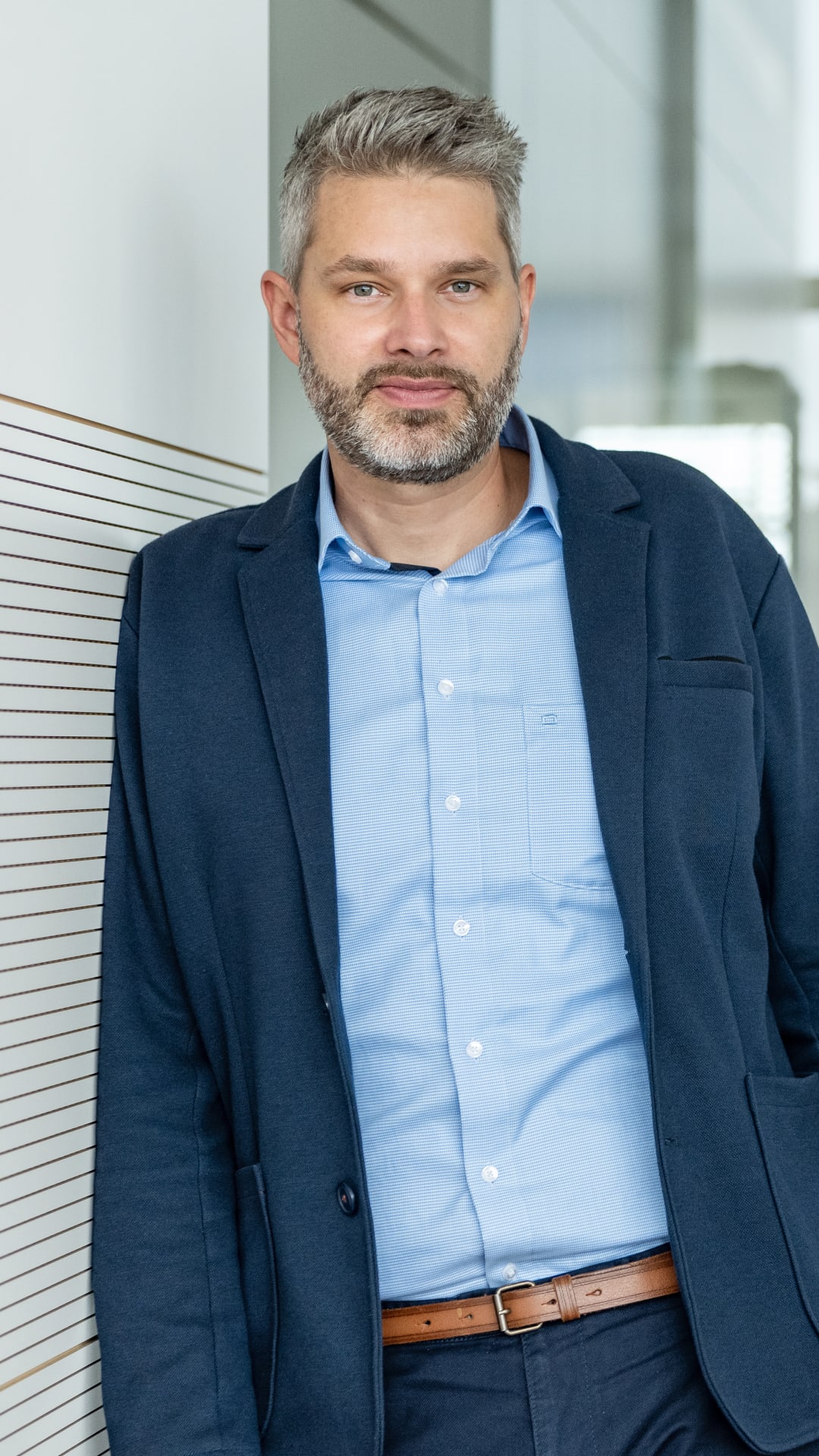
Börlind’s exciting challenges led us into uncharted territory. Developing such a compact system was also a first for Schubert. We are especially proud of the fact that it is easily on par with a large-scale system in terms of performance.
Daniel Traub
Global Key Account Manager at Schubert, March 2024
Technical Details
- TLM Power Compact filling line
- Up to 60 bottles/jars per minute
- 14 formats
- ≥ 92% machine efficiency
- Low format part costs (3D-printed parts)
- Quick set-up time < 15 min
- Fast CIP thanks to hygienic design
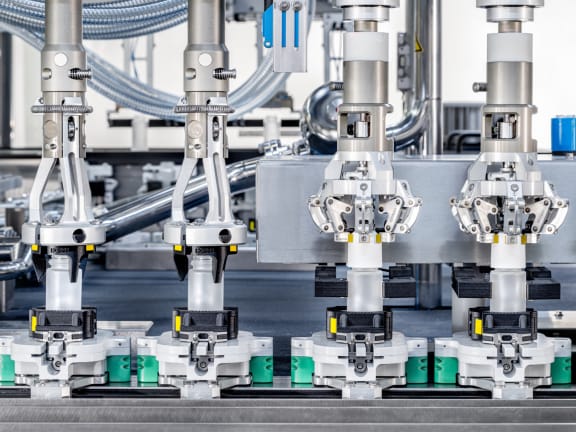
The multi-transport unit with cosmetic bottles that are sealed.
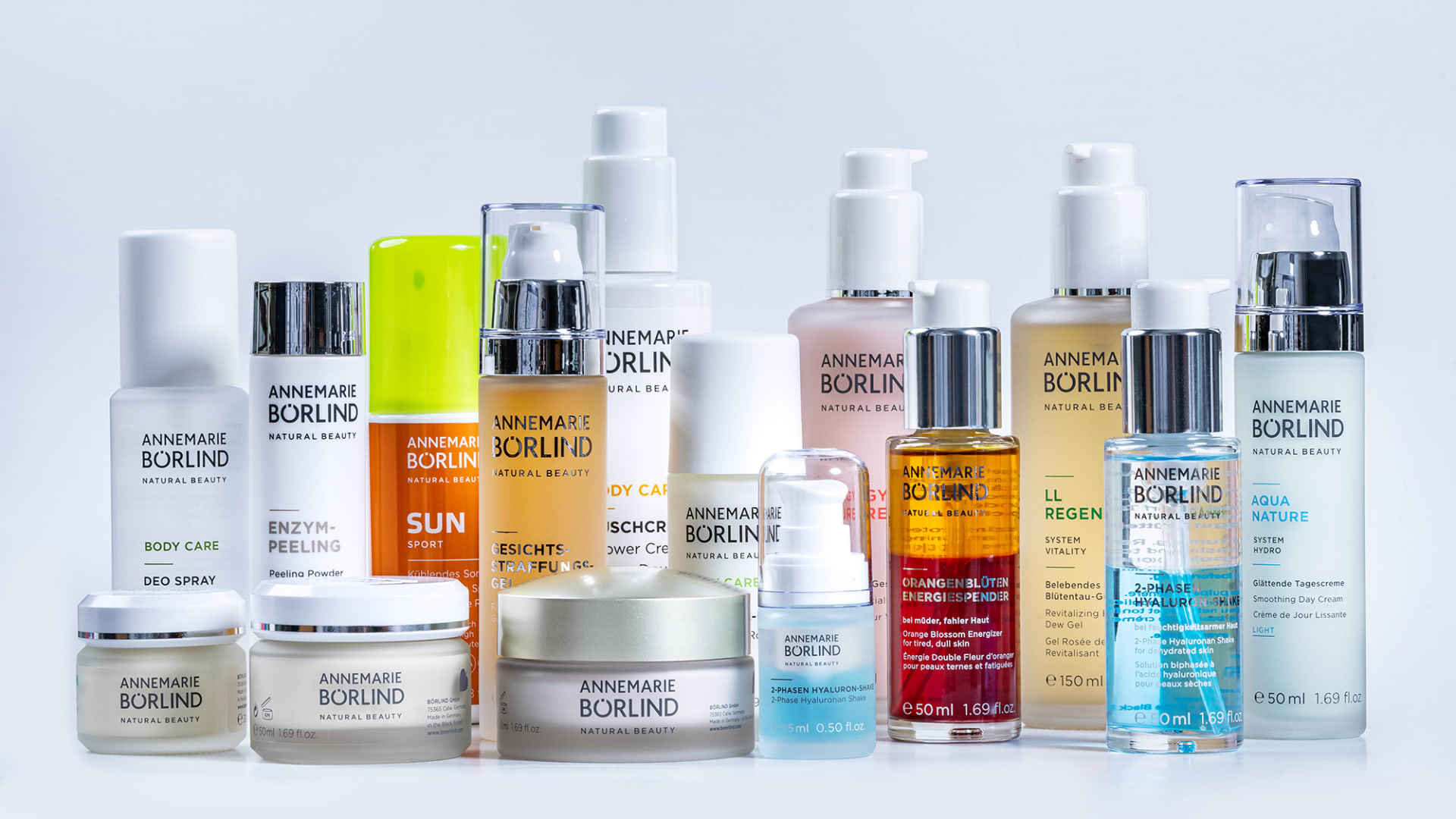
In spite of its exceptionally compact design, the new TLM Power Compact system delivers high power density in the smallest of spaces and processes a wide range of different formats.
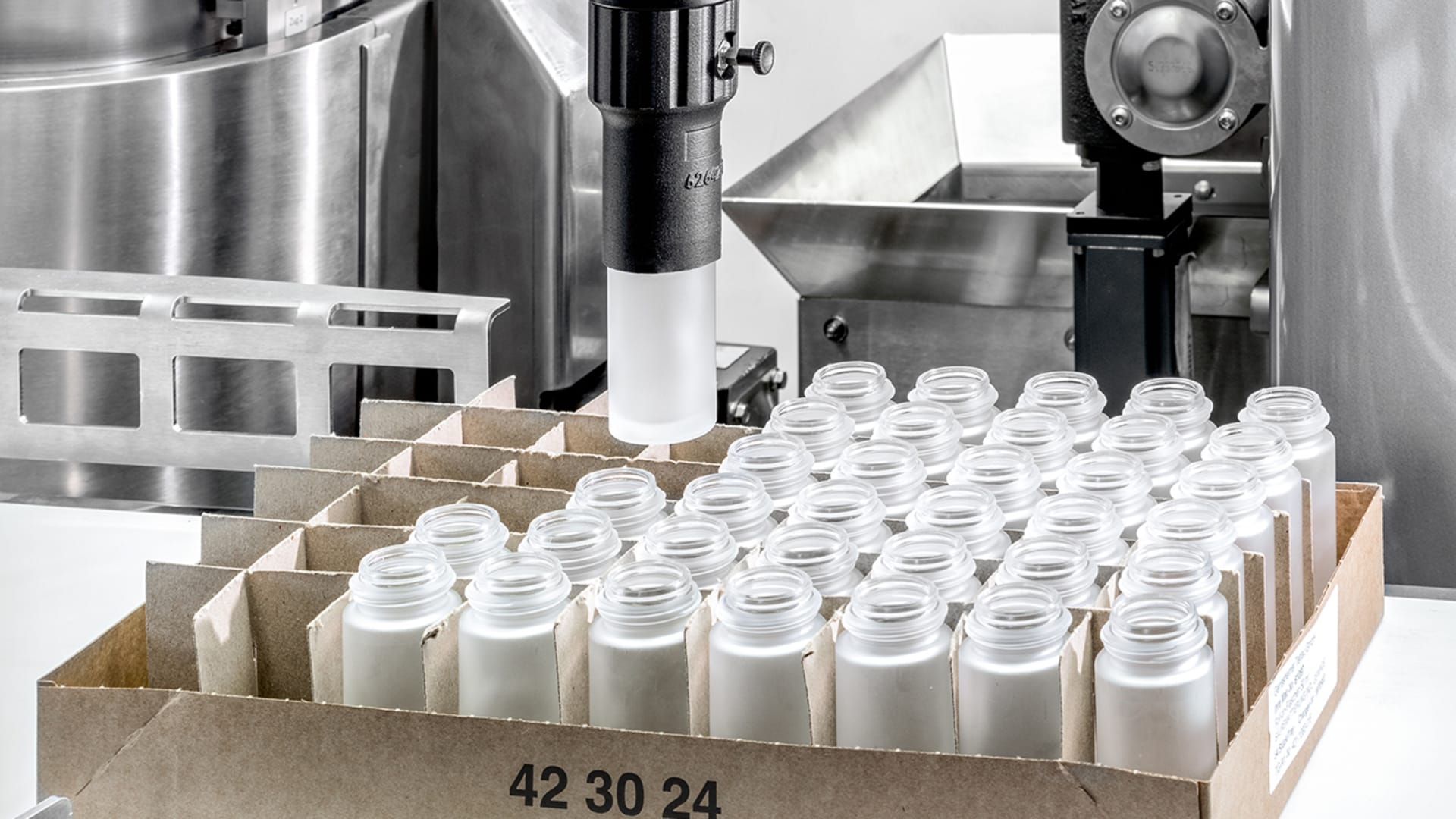
The AI-supported tog.519 cobots handle all packaging parts at the cosmetics line infeed without requiring any programming or start-up phase.
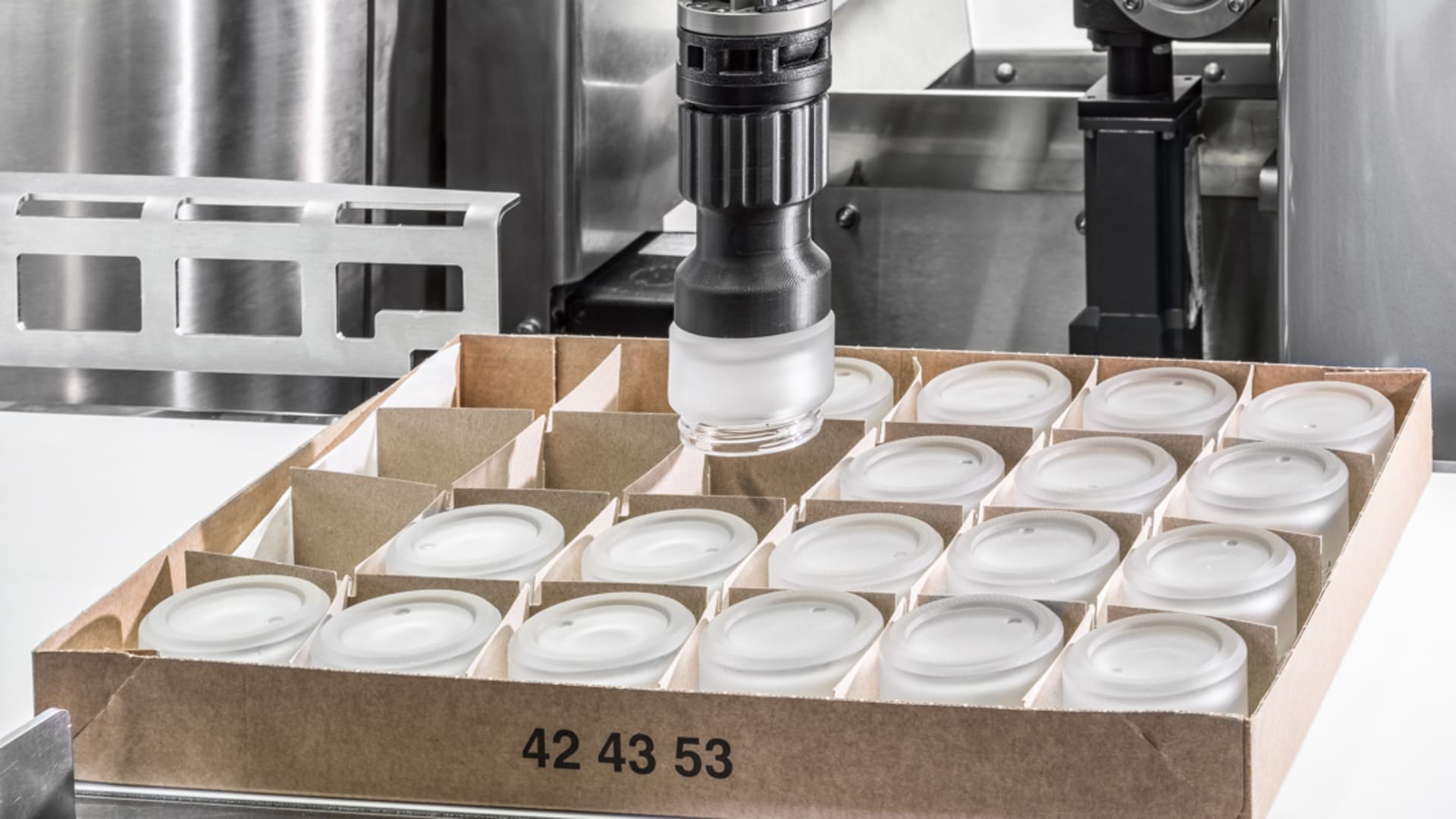
The Cobots tog.519 are extremely versatile at the infeed. Here, picking up cosmetics jars.
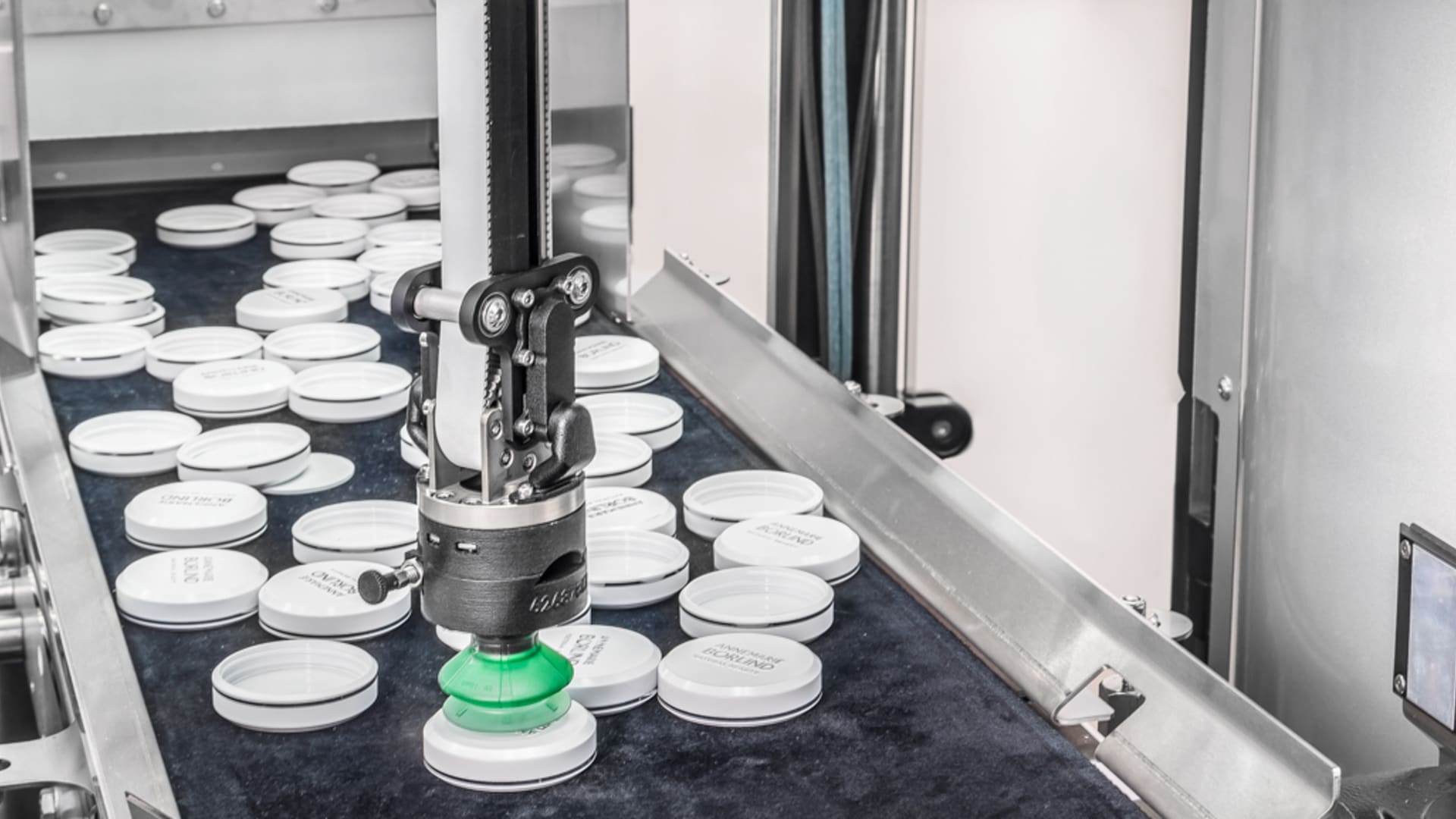
The Cobot tog.519 can pick up a wide variety of formats, such as unsorted lids for jars, without the need for complex programming.
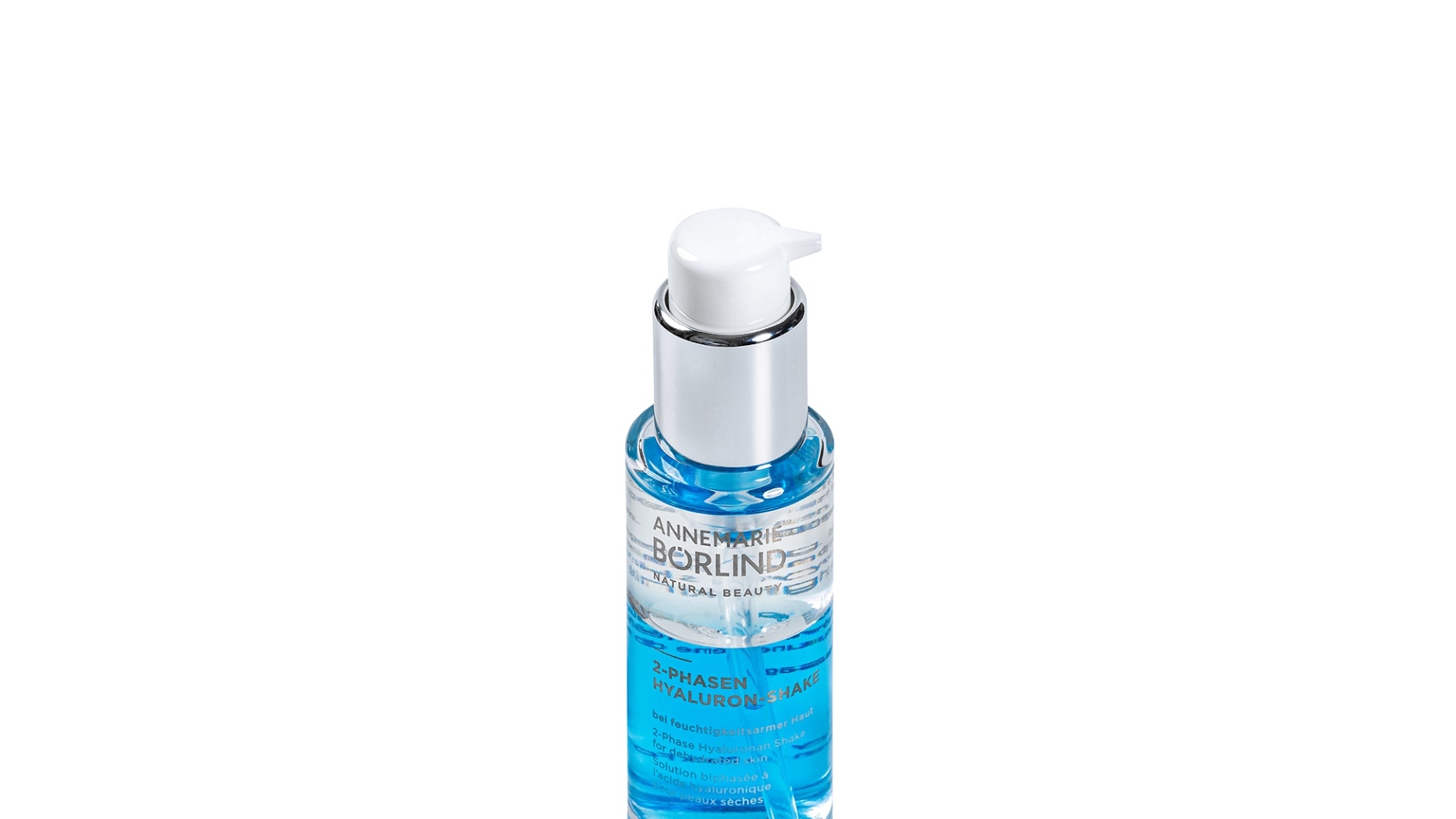
The compact filling system is used to fill glass bottles with cosmetics and seal them with pump systems.